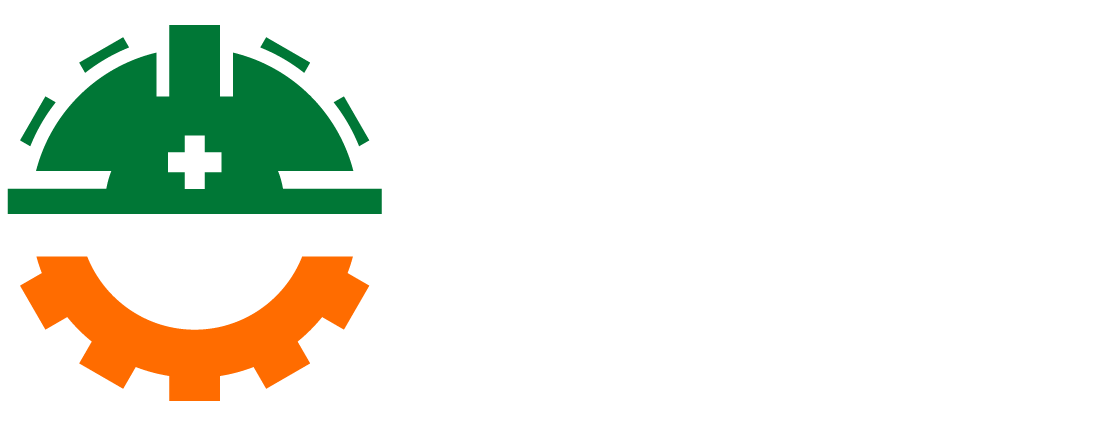
Created at: 22-02-2025 20:16
Abrasive wheels are a cornerstone tool in various manufacturing and construction sectors in Ireland. However, their use comes with significant risks that can lead to severe injuries if not managed properly. In this comprehensive guide, we will delve into the risks associated with abrasive wheels, highlight common workplace hazards, discuss potential injuries, and outline effective strategies to mitigate these dangers.
Abrasive wheels are typically used for cutting, grinding, or polishing materials, making them essential for tasks ranging from metalworking to woodworking. Despite their utility, improper handling or equipment failure can result in life-altering injuries and fatalities.
Several factors contribute to the risks associated with abrasive wheels, including:
Workplace injuries resulting from abrasive wheels can vary in severity and type, but some common injuries include:
Implementing best practices can significantly reduce the risks associated with abrasive wheels. Here are crucial strategies:
Investing in certified abrasive wheels training is paramount. Courses available in Dublin, Cork, Galway, Limerick, and Waterford ensure that workers understand:
Regular risk assessments are essential for identifying potential hazards. Ensure that:
Mandate the use of appropriate PPE among all employees operating abrasive wheels, including:
Always align practices with the manufacturer's guidelines for a specific abrasive wheel to ensure optimal safety and performance.
Working with abrasive wheels is a necessary part of many industries in Ireland, including those in Dublin, Cork, Galway, Limerick, and Waterford. However, understanding the associated risks and implementing safety measures is crucial to preventing accidents and ensuring worker safety. By prioritizing training, utilizing PPE, and performing regular risk assessments, organizations can create a safer working environment.
Encourage your workplace to enroll employees in an abrasive wheels safety course to cultivate a culture of safety and compliance. For more information on abrasive wheels training, contact us at [email protected].